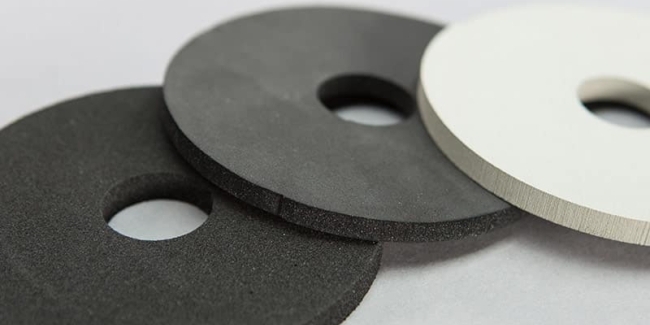
How Does The Compressibility And Chemical Resistance Of Neoprene Washers Become Ideal For Use In Mechanical And Structural Applications?
The unique combination of compressibility and chemical resistance of neoprene washers has made them a staple in many mechanical and structural applications. The synthetic rubber neoprene is made by polymerizing chloroprene. It was first produced commercially by DuPont in 1931 under the trade name Duprene. Chemically, neoprene is a type of polychloroprene elastomer. It is created by emulsifying chloroprene and performing free radical suspension polymerization.
- Comparatively, it has high tensile strength, elongation, and resilience. It gives neoprene excellent elasticity and flexibility.
- Neoprene demonstrates high resistance to degradation from oils, greases, fuels, and many chemicals. Its chemical stability is a result of this.
- The material is highly stable over a wide temperature range from -50°C to +125°C. This thermochemical stability allows neoprene to withstand heating and cooling cycles.
- Neoprene demonstrates good flame resistance and low heat conduction properties. It reduces risks from fire and burns.
- The material is easily molded and formed into a variety of shapes. It improves manufacturing flexibility.
These characteristics have led to neoprene becoming a highly versatile elastomer used in many products and industrial processes.
Compressibility of Neoprene
Its high compressibility makes neoprene an excellent candidate for gaskets, seals, and vibration dampening applications. Compressibility refers to the ability of a material to be pressed or squeezed together without a large change in volume. Materials with high compressibility conform to surface irregularities and fill gaps when compressed. Neoprene has a compressibility rating of approximately 3-7% depending on the specific grade and formulation. It means neoprene washers 3-7 mm thick compressed by 1 mm without a major increase in surface area or change in shape. The polymer chains in neoprene slide past each other under compression instead of being folded or creased.
Mechanical systems allow the material to form tight seals and make complete contact even on rough, uneven, or warped surfaces. The conformability dampens vibrations and compensates for small alignment issues or changes in dimension due to heating, cooling, or pressure fluctuations. Other rubbers and polymers are often too rigid and resist compression. When squeezed they buckle, wrinkle, or crack rather than deforming evenly. Neoprene’s exceptional compressibility characteristic is critical for its effectiveness in sealing gaskets, spacers, vibration mounts, and other applications where compression load is applied.
Chemical Resistance Of Neoprene
In addition to compressibility, the broad chemical resistance of neoprene is another essential property for its use in harsh industrial environments. Neoprene exhibits resistance to degradation from many oils, solvents, acids, and other chemicals that rapidly break down many natural rubbers. The chlorine content in the base polymer of neoprene is the key factor behind its chemical stability. The carbon-chlorine bonds present throughout the molecular structure of polychloroprene are highly stable. It prevents acids, bases, oils, and solvents from degrading or dissolving the bulk neoprene.
- Polar solvents like acetone, methanol, ethanol
- Aliphatic hydrocarbons such as fuels, mineral oils, turpentine
- Saltwater, acids, bases/alkalis
- Animal/vegetable oils and greases
Under continuous exposure at elevated temperatures above 95°C, compounds like aromatic hydrocarbons and chlorinated solvents cause swelling and deterioration of neoprene. However, under typical service conditions, neoprene vastly outperforms natural rubber in chemical environments. The chemical makeup and structure of neoprene prevent the small molecules of oils, solvents, and chemicals from penetrating and breaking up the bulk elastomer. It maintains the strength, sealing effectiveness, and vibration-dampening performance. Natural rubbers soaked with chemicals often turn soft, gummy, cracked, or brittle. Neoprene’s broad chemical resistance keeps the material intact and functional in applications like gaskets, seals, oil hoses, and fuel systems.